ヤマトの技術
Technical
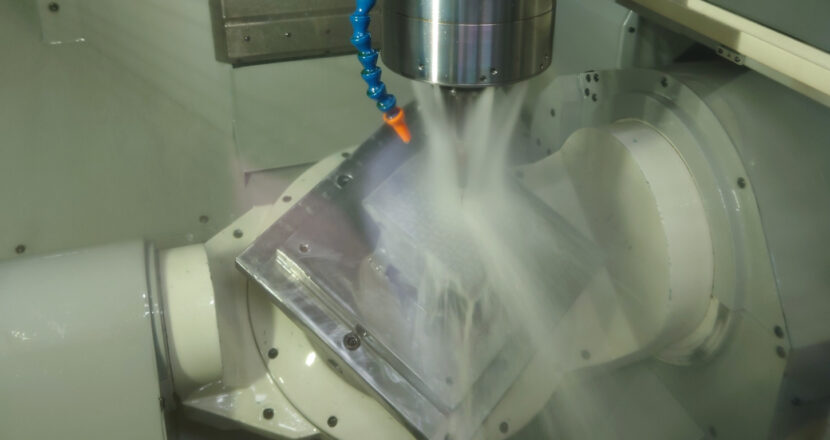
品質を追求するお客様は、どうぞヤマトへ。
ヤマト精密では、自動車や家電をはじめとした大手のお客様と長年に渡ってお取引させて頂いております。それらのお客様方から、弊社については「質が良く、納期が安定している」とのご評価を頂いております。こちらでは、安定した品質と納期を実現するための取り組みについてご紹介いたします。
加工精度
金型メーカーにとって、加工精度の維持向上は最重要課題です。そのためには工作機械を熟知し、材料ごとに最適な加工方法を選ぶことが重要です。またコスト面でも十分な検討を行い、過剰な品質によるコスト上昇も防ぐ必要があります。
加工精度の安定はまず温度から
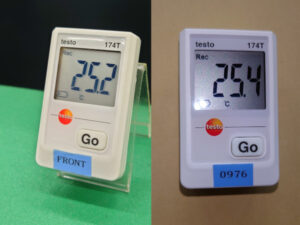
自社内に高速加工機と5軸加工機のみが入る専用のクリーンルームを整備しています。機械加工を突き詰めれば、温度変化は無視できない要因です。クリーンルーム内の各機械の前後に温度ロガーを設置して24時間温度を計測しており、温度変化による影響を分析できる体制をとっています。
加工の最適条件を求めて
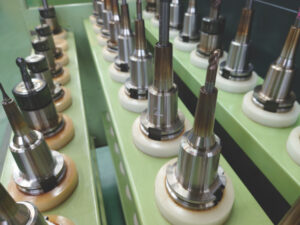
金型加工はマシニングセンターなどでの切削加工が基本です。エンドミルによって材料は削られて形作られますが、その回転数や送り、切込みピッチなどの組合せにより品質は大きく変わります。担当者曰く「刃物ごとに加工精度と表面品位に優れ、さらに刃持ちが良い最適条件がある」と言います。これを探るために、CAM担当者は機械の状況を目と耳で確認し、手で振動を感じ取って、条件の探求に勤しみます。
形状ごとの最適条件
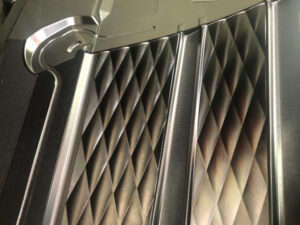
機械の動きが遅くなる微細加工、刃物が食い込む凹角周辺、ミーリングのみの磨きレス加工などでも品質を維持できるように、それぞれ微調整を行います。また、その条件は社内で共有されるため、安定した品質と高い作業効率が実現できます。ちなみに多いものでは、エンドミル1本に40通り以上の加工条件が記録されています。
選択と集中
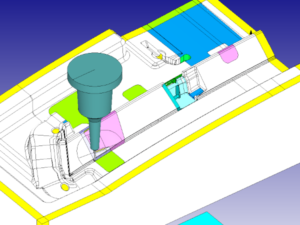
「どんな部品でも精度よく加工したい」
技術者であれば当然の思いですが、それを愚直に追い求めると手が回らなくなり、本当に必要な部分で精度が出せなくなります。加工や工程を検討するうえで、「本当にお客様が求めているのか?」という観点を持ち、限られたコストと納期で、金型の機能を最大限に向上させるために、メリハリのある加工を行います。
技術者であれば当然の思いですが、それを愚直に追い求めると手が回らなくなり、本当に必要な部分で精度が出せなくなります。加工や工程を検討するうえで、「本当にお客様が求めているのか?」という観点を持ち、限られたコストと納期で、金型の機能を最大限に向上させるために、メリハリのある加工を行います。
正しい部品は、正しく動く
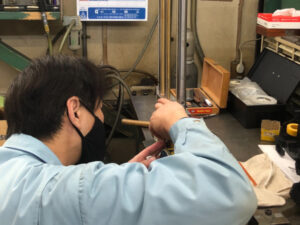
加工を終えた部品を組み立て、キャビティとコアを初めて突き合わせるとき、それまでの成果が現れます。弊社の場合、型重量3トン程度のものでは、キャビティとコアの隙間は平均0.5mm以下となっています。この程度であれば、仕上げにも手間がかからず、調整に労力を要することもありません。
現物合わせの弊害
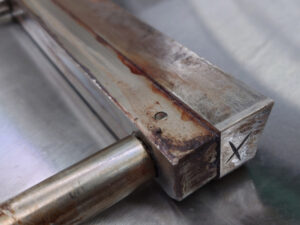
各部品のアタリが悪くても、ヤスリなどで削って調整することは可能です。しかし後から手を加えるほどに、本来の形状は崩れ、動作のムラや成型品へ悪影響を及ぼします。またそれらはトラブルの種となり、カジリ発生や、修理改造時に形状を復元できないなどの不都合が生じます。弊社の金型は、長期間の使用を前提としており、耐久性向上はもちろんのこと、修理改造時にも問題が起きないように、設計に忠実に加工を行っています。
効率化
弊社では、品質を維持しながらコスト削減と納期短縮を目的に、業務の効率化を進めています。
ミーティングによる情報共有
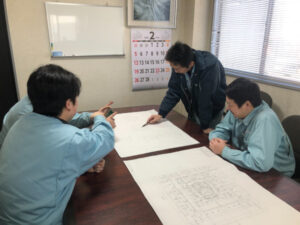
金型の部品加工では、ひとつの形状を作り上げるために複数の工程を踏み、それぞれが緊密に連帯して各自の担当部分を正確に仕上げていく必要があります。弊社では加工に携わる者が毎朝ミーティングを行い、状況を共有することで、柔軟な対応とフォローができるような体制を整えています。
初動から素早く
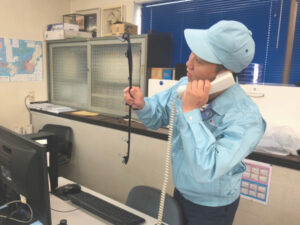
弊社では製造現場を熟知した者が営業担当をしており、営業と現場に隔たりが生じない体制を作っています。これにより、問題発生時でも状況が素早く現場に共有されるようになり、効率よく対応にあたることが可能となりました。
放電レス化
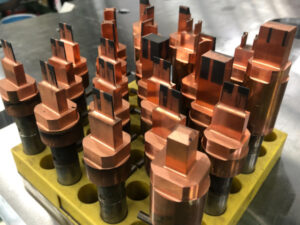
切削加工ができない深い形状で威力を発揮するのが型彫り放電加工です。しかし形状ごとにマスターと呼ばれる凸型を作る必要があり、費用と工数が増加します。これを削減するには、可能な限り切削加工で終わらせる必要があり、細径の長いエンドミルを如何に上手く使えるかが要点になります。一般的に細長いエンドミルは剛性が無く、精度や品質などで不利になりますが、長年の取り組みにより、これらを有効に使えるノウハウを蓄積して参りました。
少ないトライ回数
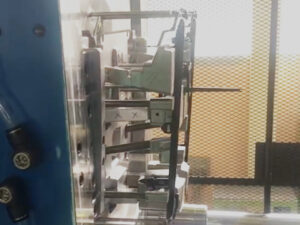
弊社の金型は、トライ回数が少ない点についてもご好評いただいております。最近の型完成までの平均トライ回数は2回程度であり、最初のトライの段階で、検証可能な成型品が取れることがほとんどです。弊社の安定した品質は納期の安定をもたらし、トライを繰り返すことによる納期遅延と費用増加を防ぎます。
技量向上
弊社では、技量向上と技術者育成の観点から、重要な業務については内製化を進めて参りました。社内での守備範囲が広がることで、タイムロス削減や納期調整、コスト抑制などの利点があります。また外注が必要な業務は、信頼できる取引先を厳選して依頼しております。
ホットランナー組付・調整
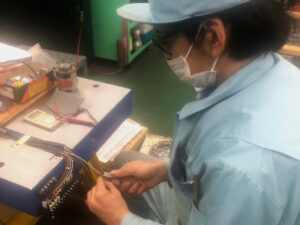
弊社では、複数のホットランナーメーカーと取引があります。その中で、お客様のご要望に沿えるものを選定し、社内で金型に組み付けます。具体的には、製品選定から配線図作成、メーカーへの発注、組み付け、調整、昇温確認までの流れを社内で行っております。また、定期的にホットランナーメーカーとのミーティングを行い、技術力の維持向上に努めています。
ホットランナーに対するこだわり
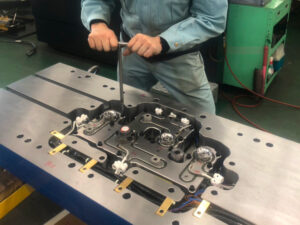
社内でのホットランナー組付けと調整を行う理由は、対応力向上にあります。配線図作成から組付けまでの全ての技術と資料が社内に揃うことで、万一のトラブル発生時にも迅速な対応が可能となります。また、ホットランナーシステムは非常に精密な機構であり、取扱いには細心の注意が必要です。それらを適切に取扱い、最大限に活用するためには、高い知識と経験が必要です。これを維持向上させるために、自社内での組付けと調整にこだわっています。
修理・改造は溶接から
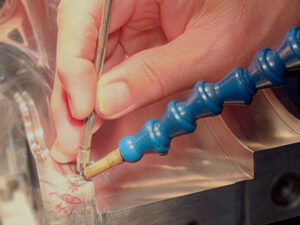
金型の修理や改造は、肉盛溶接が必要な場合が多く、このコストと納期が長年の課題でした。これを解消するため、令和3年から弊社グループ企業として、レーザー溶接部門を新設しました。こちらは三台の溶接機と熟練の人員からなる金型溶接専門のチームです。内部に溶接部門を持つことで、意思疎通の円滑化や資料の共有などが可能となり、加工部門と溶接部門の両者で作業効率が改善されました。これにより、今まで以上に品質、コスト、納期の面からお客様へ貢献できる体制になりました。
ニーズを満たすヤマトの“引出し”
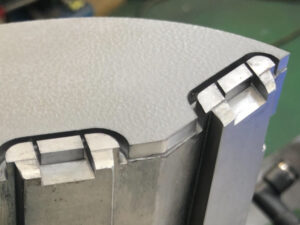
弊社は創業以来、実に多様な金型を製造して参りました。ときには成型の難しい形状や、特殊な素材によるトラブルなどにも悩まされました。社内で納得のいく解が得られないときは、その分野で技術を持つ企業と繋がり、広く知見を求めることで、それに対応して参りました。その結果、良質な信頼できる取引先と繋がることができ、弊社の“引出し”を増やすことにつながりました。もし、お使いの金型に問題を感じておられましたら、ぜひ弊社にご相談下さい。